ER COLLET
₹260.00
Precision Machining
ER collets are essential components in the realm of precision machining, known for their versatility and reliability in holding cutting tools and workpieces securely in place. Developed in the 1970s by Fritz Fenner, ER collets have become a standard in various industries, from automotive and aerospace to woodworking and manufacturing. This guide will delve into what ER collets are, their types, applications, and the benefits they bring to precision machining.
What is an ER Collet?
An ER collet is a type of tool holder used primarily in CNC (Computer Numerical Control) machines, lathes, and milling machines to secure cutting tools, drill bits, or workpieces. The name “ER” stands for “Elastic Rubber,” which refers to the collet’s ability to flex and grip tools of various sizes within a specified range. ER collets are known for their concentricity and ability to hold tools tightly, reducing runout and ensuring precision.
Types of ER Collets
ER collets come in various sizes, each designated by a number that indicates its size range. The most common sizes include:
- ER8: Smallest size, suitable for holding small tools and drill bits.
- ER11: Common in small machining applications.
- ER16: Versatile and widely used for medium-sized tools.
- ER20: Suitable for a wide range of applications.
- ER25: Popular for larger tools and heavier machining tasks.
- ER32: One of the largest standard sizes, used for heavy-duty applications.
- ER40: Largest standard size, providing maximum gripping force and stability.
Components of an ER Collet System
An ER collet system consists of three main components:
- ER Collet:
- The actual gripping component that holds the tool or workpiece.
- Made of high-quality, hardened steel to withstand wear and provide a secure grip.
- Collet Nut:
- The nut that holds the collet in the collet chuck.
- Designed to tighten the collet around the tool as it is screwed into the chuck.
- Collet Chuck:
- The holder that fits into the spindle of the CNC machine or lathe.
- Houses the collet and collet nut, providing a secure and precise tool-holding solution.
How ER Collets Work
ER collets work by compressing around the tool or workpiece when the collet nut is tightened. The tapered shape of the collet fits into the matching taper of the collet chuck. As the nut is tightened, the collet is drawn into the chuck, causing it to contract and grip the tool evenly along its entire length. This uniform gripping action minimizes runout and ensures high precision and stability during machining.
Applications of ER Collets
ER collets are used in a wide range of applications, including:
- CNC Machining:
- Holding cutting tools, end mills, and drill bits with high precision.
- Used in milling, drilling, and tapping operations.
- Lathes:
- Securing workpieces for turning operations.
- Ensuring concentricity and stability during high-speed rotations.
- Woodworking:
- Holding router bits in woodworking CNC routers.
- Providing accurate and repeatable tool changes.
- Engraving and Milling:
- Used in precision engraving and micro-milling applications.
- Ensuring fine detail and accuracy.
Benefits of ER Collets
ER collets offer several advantages that make them a preferred choice in precision machining:
- Versatility:
- Capable of holding tools with a wide range of diameters.
- One collet can grip various tool sizes within its range, reducing the need for multiple collets.
- Precision:
- High concentricity and minimal runout ensure accurate machining.
- Consistent gripping force along the tool’s length enhances stability.
- Ease of Use:
- Simple to install and change tools quickly.
- Reduces downtime and increases productivity.
- Durability:
- Made of hardened steel to withstand the rigors of machining.
- Long-lasting and resistant to wear.
- Cost-Effective:
- Reduces the need for multiple tool holders.
- Provides reliable performance, minimizing tool replacement costs.
Conclusion
ER collets are indispensable tools in the world of precision machining, offering versatility, precision, and ease of use. Whether in CNC machining, lathes, or woodworking, ER collets provide a reliable and efficient solution for holding tools and workpieces securely. Their ability to grip a wide range of tool sizes with high concentricity and minimal runout makes them a valuable asset in any machining operation. Understanding the types, applications, and benefits of ER collets can help machinists and manufacturers achieve greater accuracy, productivity, and cost savings in their operations.
Did you like this product? Add to favorites now and follow the product.
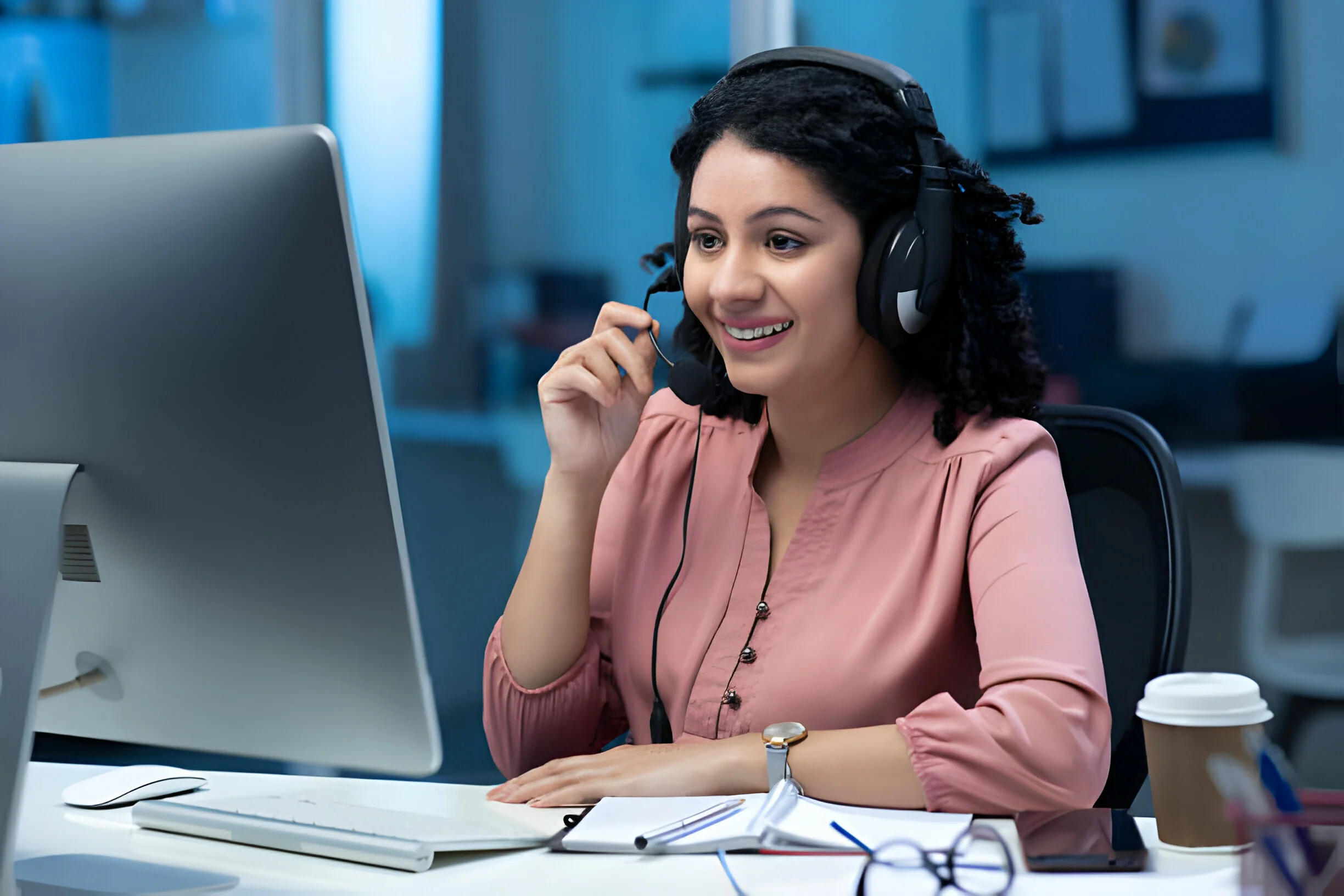
(+91) 96008 30881 Start Live Chat
Description
“ER” name came from an existing “E” collet which named as Rego-Fix modified and appended “R” for “Rego-Fix”. The series number is the opening diameter of the tapered receptacle, in MM
Part No | Collet Type | BORE RANGE Min to Max | Ødiameter(mm) | Length in mm | PART NO.EXAMPL |
1 | ER-11 | 2 to 7 mm in steps of 0.5mm | 11.5 | 18 | ER11 5 mm |
2 | ER-16 | 2 to 10 mm in steps of 1mm | 17 | 27.5 | ER16 8 mm |
3 | ER-20 | 2 to 13 mm in steps of 1mm | 21 | 31.5 | ER20 8 mm |
4 | ER-25 | 2 to 16 mm in steps of 1mm | 26 | 34.5 | ER25 8 mm |
5 | ER-32 | 3 to 20 mm in steps of 1mm | 33 | 40 | ER32 8 mm |
6 | ER-40 | 4 to 26 mm in steps of 1mm | 41 | 46 | ER40 8 mm |
Additional information
Weight | 0.5 kg |
---|---|
Dimensions | 30 × 50 × 20 cm |
brands | Shell, 25 |
Reviews
There are no reviews yet.